Pace of technology scaling & associated infrastructure for plastics recycling
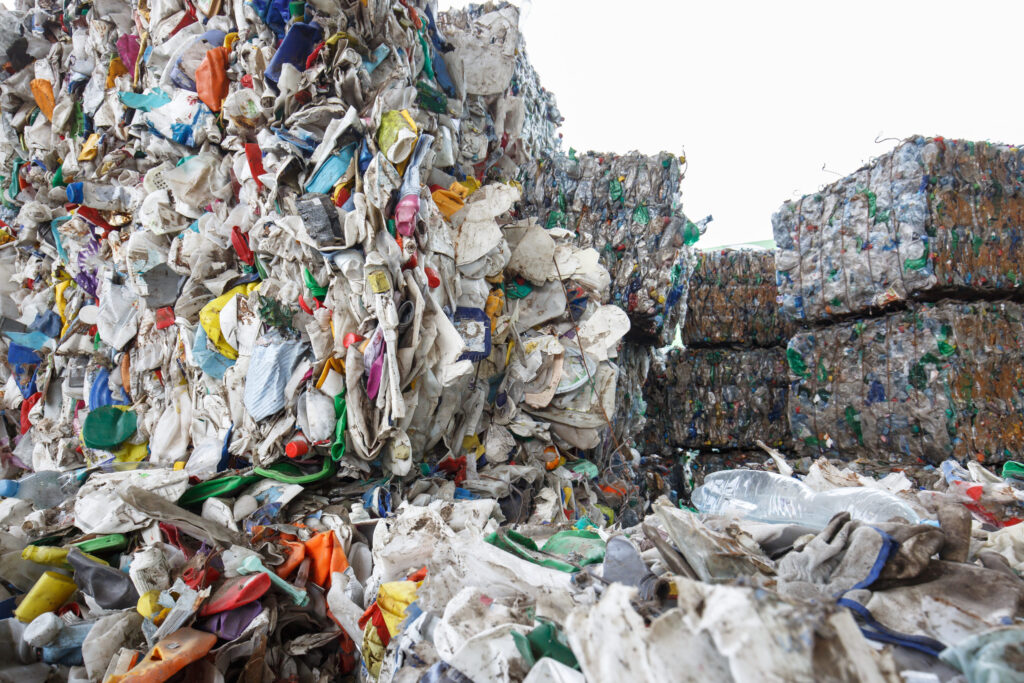
Scaled plastics recycling technology and associated infrastructure does not currently exist as critical infrastructure elements – including collection, sorting, processing, and end-use application facilities, and their harmonization – remain in the very early stages of development in many ecosystems. Even in developed regions, waste collection streams and systems are dispersed with relatively low-input volumes compared with the requirements needed to achieve economies of scale. A significant portion of plastics waste lacks suitable quality for mechanical recycling, especially for incumbent virgin polymer replacement in applications such as food packaging. Today, many collection systems are under economic pressure and are overwhelmed with waste volumes of all materials and gaps in supply and end-use demand for recycle material remain.
Different technologies exist to recycle plastics, and each has strengths and weaknesses. Mechanical recycling technologies have matured and possess favorable attributes such as lower CAPEX requirement, lower operating costs for achieving breakeven economics, and lower CO2 emissions. However, mechanical recycling is restricted by reduced feedstock flexibility and degradation of plastics after every recycling cycle; so, while the potential impact of mechanically recycled plastics is significant, those volumes fall well short of addressing the total disposition of plastics waste. Chemical and other recycling technologies such as solvent solution/dissolution, depolymerization, pyrolysis and gasification can produce recycle content without degradation of properties. However, widespread commercialization of these technologies has not yet been achieved. Pyrolysis and gasification technologies can process multiple low-quality waste feedstock streams; however, these technologies have high CAPEX requirements, long breakeven time, and scope 1 & 2 CO2 emission issues. Depolymerization (hydrolysis, glycolysis, and methanolysis) capable of producing monomers are favored by low CO2 emissions and breakeven economics, but these technologies are limited to condensation polymers such as PET. Enzymatic recycling can produce monomers, but currently it is at a nascent stage.
The economics of fully scaled recycling technology is not clear and will need government incentives and policy support to realize economic viability in a timely fashion. Leading stakeholders are actively looking for technology to affect transformation of assets and logistics while policy makers and investors continue to seek a clear vision for future infrastructure. Transformative technologies have great potential for the management of municipal solid waste, including plastics and, as innovation accelerates, technology trends start to converge and synergies between these technologies will drive exponential, rather than linear, change. Seemingly disconnected activities – consumption, disposal, collection, processing, production – can suddenly merge as an integrated system, assuming stakeholders align values to achieve a common goal. Understanding the opportunities and the impacts of these technologies requires an understanding of the various technologies and the pace at which they are developing.
By 2050, a minimum of $1.3 trillion investment is required to attain complete circularity of plastics, representing a 15% increase over a business-as-usual, linear model. In order to meet the growing demand for recyclate, mechanical and chemical capacity additions are expected to increase by 2x and 2.5x respectively. Accordingly, more than half of the $1.3 trillion investment would be required to build the recycling capacities while 60-65% of the total investment would be required to build polyolefin capacities (both virgin and recycling). The technologies still in early phase of development are currently not only limited by scale and yield factors, but by the requirement of a higher quality waste feed. Pyrolysis technologies (both catalytic and non-catalytic) have the highest number of developments while gasification, solvent solution/dissolution, and glycolysis/hydrolysis account for 1/3rd of the remaining developments. Microwave-based pyrolysis, methanolysis, enzymatic routes, and hydrothermal liquefaction currently draw scarce interest. Technology buildouts will align to the type of plastics targeted, with mixed plastic waste, particularly for polyolefins, having the largest share, followed by gasification and depolymerization (hydrolysis, glycolysis and methanolysis). The technologies still in early phase of development are currently not only limited by scale and yield factors, but by the availability of a higher quality waste feed. North America and Europe would have the early mover advantage with the majority of current facilities and collaborations operating and announced in these regions. Remaining developments are accounted for by Asia and Australia, with a few announcements in South America. Though mainland China and Indian sub-continent would have most of the overall capacity additions, these capacities would primarily be focused on virgin production. Europe and North America regions are expected to have more than 80% of their capacity additions dedicated to recycling.
Are you attending AFPM IPC? Join us at our Chemical Market Seminar: Conquering Market Turbulence on Sunday, 26 March 2023 from 1 PM – 3 PM Central Time at the Marriott Rivercenter Hotel. Our thought leaders will provide an in-depth overview of the challenges and future opportunities for the Olefins and Polyolefins, Aromatics, Inorganics, and Syngas sectors.
Register now and secure your place: Conquering Market Turbulence
Robin Waters
Research & Analysis Director, Circular Plastics Service
Chemical Market Analytics by OPIS, a Dow Jones Company
The Circular Plastics Service, enables you to understand government regulations and policies, prepare a plan to mitigate risk, determine which part of your company is most vulnerable, and assess opportunities for investment.